PRODUCTS
Technology of vacuum air servo stages
Key technologies in vacuum air servo stages
■ Compact, with linearity and rotation capabilities in one unit
■ Higher productivity: seamless positioning/load control switching
■ Delicate control after contact
Air servo technology
The air stage can be modeled using a third-order delay system. A PDD2 control system is used for control. Thus, velocity/acceleration signals are generated from position measurement value signals, and the multiplexed feedback loop consists of position, velocity, and acceleration signals. Moreover, feedforward compensation generated from the inverse model is added to improve tracking.
A disturbance observer is employed to compensate for cable carrier or other disturbances, enabling highly precise positioning, and linear compensation is applied to compensate for modeling errors from nonlinear elements associated with pneumatic systems.
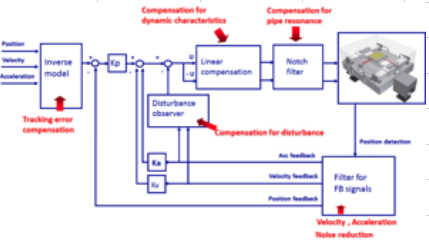
Yaw control
Yaw attitude is controlled by driving a dual-axis actuator. For yaw attitude control during operation, the yaw angle is calculated from the position detection value of the axis that is open a certain distance. As for effectiveness of compensation under vacuum, yaw angle deviation does not exceed 1 μrad, with repeatability not exceeding 0.5 μrad.
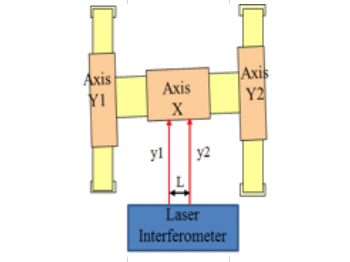
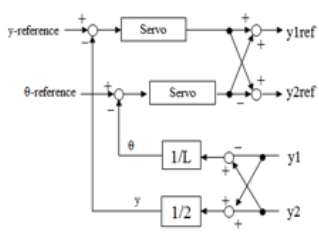
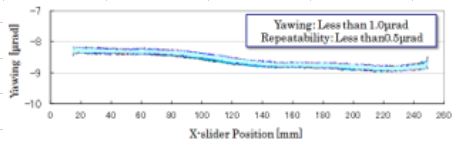
Disturbance observer
As a control technology for eliminating disturbance factors such as cable tension or friction, the disturbance observer applies our proprietary control algorithm. This enhances tracking accuracy and compensates for disturbance vibration from acceleration and for disturbance force such as cable load (spring load).
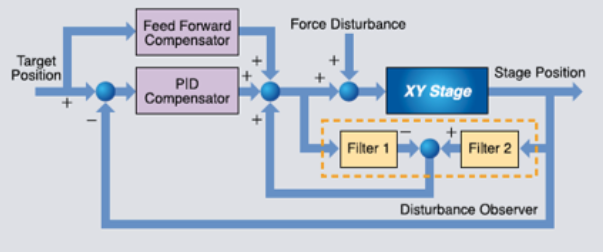
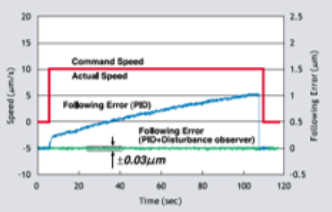
Data from scanning at low speed
Air bearings and three-stage exhaust system
Fully non-contact operation is possible, with the slider floating by means of air bearings on each surface. This enables high-precision operation with high repeatability. With a three-stage exhaust system, the air supplied to the air bearings can be released from the differential exhaust grooves on the slider inner surface via a dry pump. As a result, pressure at the ends of the slider can ultimately be reduced to about that of a medium vacuum. This way, pressure in vacuum chambers can be maintained to be high vacuum with a fully non-contact actuator that works under vacuum.
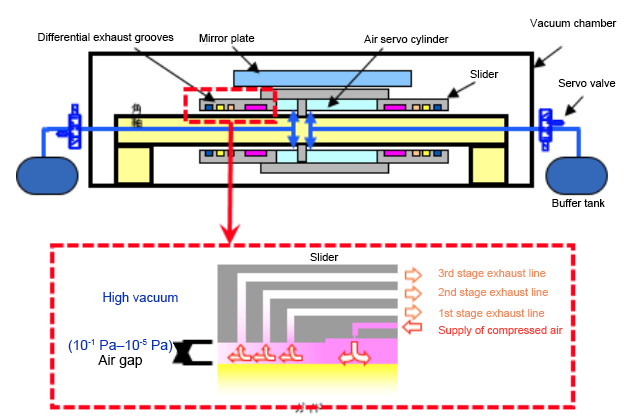
Pitch error correction
This error correction for measurement values makes internally measured values of the position measurement signal processing unit as close as possible to actual values (as measured externally). Specifically, the correction applies to errors in position detection values due to sensor precision, structural distortion of the equipment (such as dimensional errors of materials or distortion from assembly), and errors from misplaced workpieces. Fast, hardware-accelerated error correction is possible by measuring and entering correction table information in advance. Multiple error corrections are available for straightness, perpendicularity, and more.

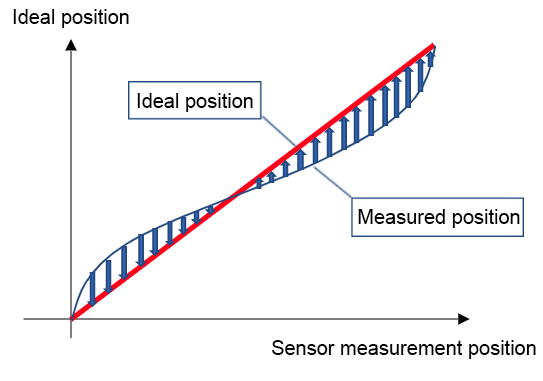